First impression of the Anet A6
Anet is now one of the best-known 3D printer manufacturers from China. In addition to the slightly less well-known "Anet A6", the manufacturer also sells the much more well-known model "Anet A8" as well as other ready-made printers, which, however, are in much higher price categories. This test deals with the Anet A6. First, let's take a closer look at the most important differences between the two inexpensive Anet models.
Anet A6 vs. Anet A8
Both models are 3D printer kits that differ mainly in the details. Probably the most relevant difference between the Anet A6 and the Anet A8 is the larger display of the A6 and the one-button control. The display of the Anet A6 shows up to 12864 pixels, whereas the display of the A8 only has 2004 pixels. The Anet A8 is operated via 5 control buttons. The Anet A6, on the other hand, has a one-button operation with rotary control. The mainboard used is now identical in both models.
- Anet A6
- Anet A8
Another difference is the guidance of the X-axis. The A8 has a vertical guide, so both shafts run parallel on top of each other, whereas the shaft guide of the Anet A6 runs horizontally, i.e. next to each other. All brackets of the A6 are made of acrylic. Brackets of the A8 model were partially created using 3D printing. There is another difference in the scope of delivery. The A6 comes with a 500g roll of white PLA filament. This was not done with the Anet A8!
What's in the box
The Anet A6 kit is delivered with all necessary components. In addition to the housing parts, the required screws, belts, shafts, guide rods, etc. are also included. The tools required for assembly are also included in the scope of delivery, so that even those who do not have the appropriate tools at hand can assemble the printer kit without any problems. The manufacturer even includes a 500g roll of white PLA filament with every Anet A6 kit. After assembly, nothing stands in the way of a first attempt at pressure.
Design and workmanship
The Anet A6 was created based on the Prusa design by Josef Prusa and can largely be assigned to the RepRap scene ("Rapid Prototyping and Rapid Manufacturing"). The open source design would make it possible to reproduce the Anet A6 without the finished printer kit.
The processing of the printer is good according to the price. In the tested kit no parts had to be reworked, as well as the parts fit together and screwed. The included steel shafts were straight and could be easily installed. Nevertheless, these DIY Printer Kits from China are always to be treated with caution. The components of our test kit were knotless, but it is not uncommon to catch inaccurate waves, a distorted heatbed or other, badly processed parts!
Hardware
The print space of the Anet A6 measures 220 x 220 x 250 mm. The extruder is of the "Direct Drive" type, in which the extruder is located directly above the hotend and thus leads to an increased weight on the X-axis. The nozzle has a diameter of 0.4 mm. The printable layer height is between 0.1 and 0.2 mm. 1.75 mm filament made of different materials is supported (ABS / PLA / HIPS are mentioned). Anet specifies the accuracy of the X and Y axes as 0.012 mm. The Z-axis is 0.004 mm. The motors used are unspecified NEMA17 stepper motors. The mainboard is of the type Anet V2.0.
Assembly of the Anet A6
Well, where are the instructions? The Anet A6 kit does not come with printed construction instructions. Instead, Anet includes a USB card reader in the form of a stick with a suitable 16GB Micro SD memory card. In addition to the illustrated assembly instructions, the memory card also contains the “Cura” slicer program, the appropriate printer drivers and test files that are tailored to the A6 and can be printed out immediately after assembly.
The instructions provided are mostly illustrated, but it is advisable, especially for beginners, to follow the video instructions on YouTube. The step to the Z end stop was even completely omitted in the illustrated instructions, which would certainly have led to a lot of frustration at the end of the assembly. But you shouldn't rely 1: 1 on the manufacturer's video instructions either. The carrier of the heatbed is mounted the wrong way around in both instructions, which means that the belt does not run parallel.
The assembly of our test copy you can watch in this video.
Calibration of the Anet A6
Before you can even start printing, the printer has to be calibrated. The Z and X axes must run parallel, the heat bed of the Y axis must be in the lead and the distance between the nozzle and the heating bed must also be adjusted. The height of the heating bed can be corrected using four threaded screws with wing nuts. The maximum distance to the nozzle should not be more than 0.1 mm. To achieve this distance, take a sheet of paper and place it on the heating bed. If you run the nozzle over it, you should be able to feel a slight pressure on the sheet. All printer belts should be sufficiently tensioned, otherwise the printing results will be inaccurate.
Another step is to insert the filament. In order to gain initial experience, you can safely use the supplied filament. The filament is fed directly into the extruder. To do this, the metal spring rocker is pressed down and the filament is pushed through the small opening. Then you have to insert the filament past the transport wheel through another opening directly into the nozzle with a little feeling. You can tell whether the filament has been inserted correctly by whether liquid filament is coming out of the nozzle. Of course, you should preheat the nozzle to around 200 ° C beforehand! The filament can be removed by pushing a few centimeters through the preheated nozzle, pressing down the rocker and pulling the filament upwards with a swing.
For a better illustration, here is another video about the calibration of the Anet A6
First pressure tests
If you have carried out the above steps correctly, nothing stands in the way of the first print. For beginners it is advisable to first print the print files provided on the SD card. For printing, the SD memory card is inserted into the corresponding slot on the mainboard. Then you switch on the Anet A6 and select the SD memory card as the print medium. Alternatively, you can also print from a connected computer. A connection between the computer and the printer is established via the USB interface on the mainboard. The required drivers are also located on the SD memory card.
Once you have started a print job, the heating bed and the nozzle will heat up to the temperature specified in the GCODE file. The current temperature can be read and monitored via the display. The temperature of the heating bed is usually between 50°C and 60°C. The temperature of the nozzle depends on the respective filament. The vast majority of filament manufacturers provide the appropriate printing temperatures. The printing temperatures are also indicated on the included Anet filament. But here too, you have to try it out! During our first printing tests, the heating bed was set to 50°C and the nozzle to 200°C by default. However, we achieved better printing results with the Anet filament at 60°C and 210°C. A recommended first attempt at printing would be the “XYZ Calibration Cube”. This small cube is printed quickly and the accuracy of the print can be measured with a caliper.
Our first printing experiences with the Anet A6 are more than positive. If you observe all the steps for commissioning, the first print attempt can also be successful and provide an accurate result. Compared to much more expensive ready-to-use printers, the print result of the Anet A6 is in no way inferior to this.
You can download a GCODE for the XYZ Calibration Cube tuned to the Anet A6 here: https://www.dropbox.com/s/u5dtx1a989sivrw/AA_xyzCalibration_cube.gcode
CAD and slicer
You create your own 3D models using so-called “CAD programs”. One of the most beginner-friendly is "TinkerCAD" , a "browser-based 3D design and modeling tool". Here you can start modeling straight away without even having to download any software and export your finished 3D model as an STL file. Advanced users should take a look "SketchUp" throw. This free 3D program is more complex, but also offers a lot more modeling options.
- TinkerCAD
- SketchUp
Once you have created a 3D model and saved it in STL format, you need a so-called “slicer program” to create a printable GCODE from it. The most famous freeware 3D slicer is "Cura" , If you have downloaded and installed Cura, you have to create a new 3D printer profile with the appropriate Anet A6 parameters. Beginners can also work on the finished Profile of "maciekish" To fall back on. The 3D model in STL format is now imported into Cura. Numerous print parameters can then be set. In addition to the speeds, the layer height, the infill and other parameters can also be given as GCODE. In addition, you get a preview of how the print will run, what time it will take and how much filament will be used. The GCODE can be exported to the SD memory card or you can print directly via Cura, provided that Cura is connected to the Anet A6 via the USB interface.
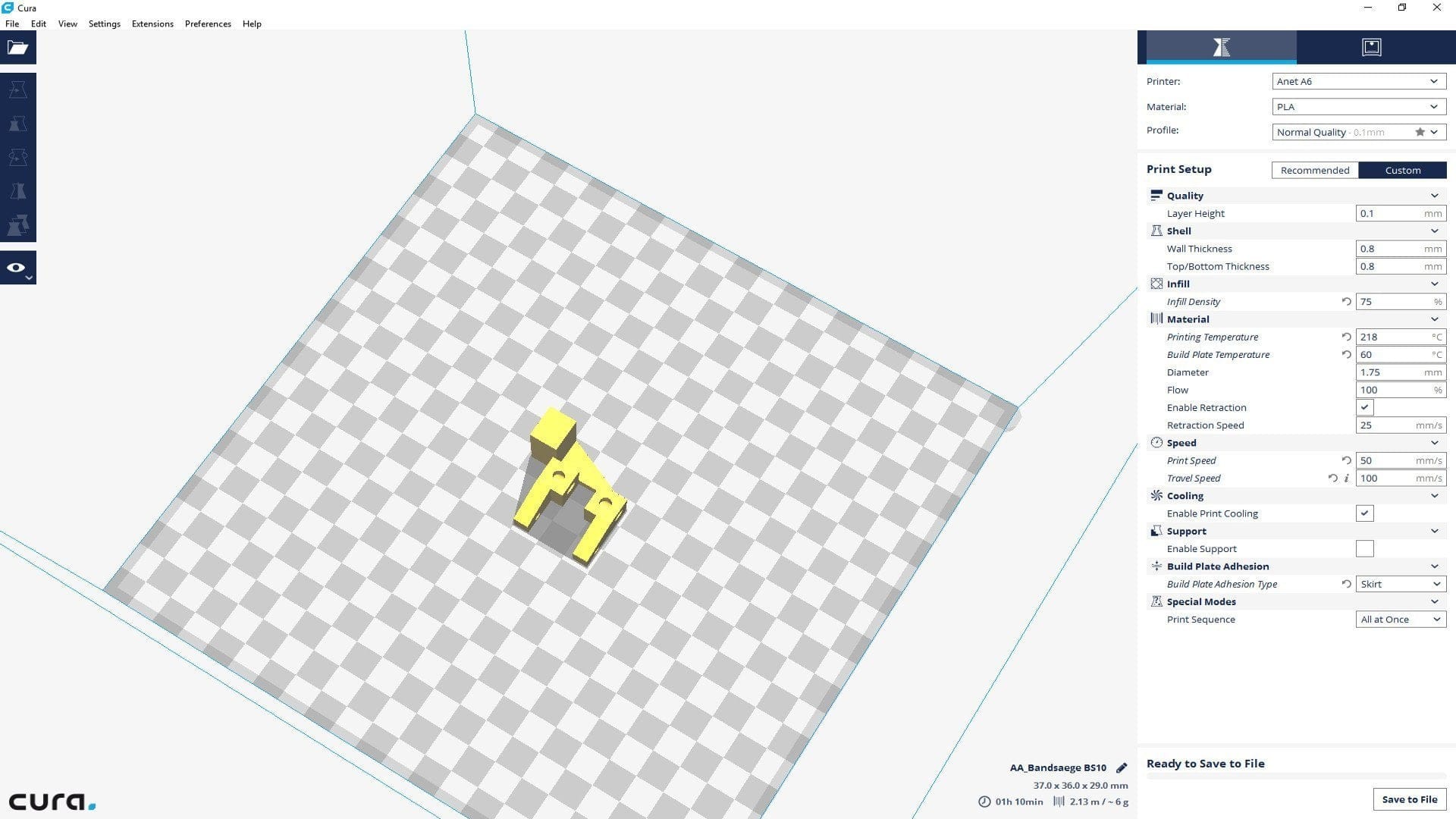
Cura3D
Anet A6 improvements
A DIY 3D printer is often an extensive handicraft project in which you like to exchange parts in order to achieve even better printing results. On the one hand, there are printable improvements that are comparatively easy to implement, but there are also extensive modifications that change the former Anet A6 extensively. You can find an overview of possible modifications attached. We have already tested many of the improvements listed here in detail.
Printable improvements
Fan duct (fan): This improvement ensures a uniform cooling of the filament and is one of the most important, printable improvements.
Y-Belt Tensioner: So that the belt of the Y-axis is always tight, it is advisable to print this belt tensioner.
Y-Belt Tensioner by Photograaf16
X-Belt Tensioner (belt tensioner): Also, the belt of the X-axis should not be loose. A good solution provides this belt tensioner.
X-Belt Tensioner by vernierroger
Table Nut Cover: With this improvement, the heating bed is even easier to calibrate.
Tablet Nut Cover by AndrewUsov
Filament Guide: So that the filament does not get tangled there is this practical filament guide, which leads the filament evenly to the extruder.
Tablet Filament Guide by CanalVap
Replaceable improvements
Igus plain bearings (RJ4JP-01-08): One of our first, non-printable improvements was the replacement of the original ball bearings with the Igus slide bearings RJ4JP-01-08. The all-plastic plain bearings consist of a special iglidur® plastic that is particularly wear-resistant and also self-lubricating. The advantage of the Igus plain bearings compared to the factory-installed LM8UU linear bearings is the reduced volume and freedom from maintenance. To convert to the Igus RJ4JP-01-08 you need a total of 8 such plain bearings, which are available from € 2 per piece.
Igus Precision Aluminum Shaft (AWMP-08): The steel shafts contained in the Anet A6 printer kit are not of particular quality. If you are looking for an inexpensive alternative, it is advisable to take a look at the Igus precision aluminum shafts. These anodized full aluminum shafts are available directly from Igus from € 8.65 per meter. Of course, you can also have the waves cut to the right size. In our test, the X-axis shafts were exchanged for two AWMP-08 and four Igus RJ4JP-01-08. Although the slide slides more difficultly on the X-axis, the reduced volume is clearly noticeable. The print result also feels more accurate.
GT2 Timing Belt and Washers: A worthwhile improvement is the replacement of the original timing belts and pulleys. Unfortunately, Anet used a very stiff toothed belt, which wears off comparatively quickly with increasing tension. It is also interesting to switch to pulleys with 20 teeth. Pulleys with more teeth allow a higher printing speed. A pulley with fewer teeth, on the other hand, enables a more precise print result. If you change the pulleys and the toothed belt, make sure that the steps are still set correctly.
- 16 teeth: 100 steps / mm
- 20 teeth: 80 steps / mm
- 25 teeth: 64 steps / mm
E3D-V6 Bowden: It is also interesting to convert the direct extruder to the E3D-V6 Bowden extruder. The advantage of a Bowden conversion is the lower weight on the X-axis, which means that more accurate prints can be achieved at higher printing speeds. At the same time, however, the distance between the extruder and the nozzle is increased, which means that very soft filaments in particular are very difficult to print with a Bowden set-up. If you would like to change, we recommend an E3D-V6 Bowden extruder replica, which is available from € 7. Of course, the X-axis slide must also be converted to Bowden accordingly. A very good design with a nice name "Frankenstein" is available on thingiverse.
Inductive / capacitive proximity sensor: Constantly reorienting the heatbed can quickly become frustrating in the long run. A capacitive or inductive proximity sensor, which replaces the Z end stop, can help. The proximity sensor is attached directly to the extruder carriage. It is then no longer necessary to manually correct the distance between the nozzle and the heatbed. However, in order for such an "autolevel" conversion to be successful, a different firmware must be flashed onto the mainboard of the Anet A6. The most well-known alternative firmware for the Anet A6 and Anet A8 printer series is the so-called "SkyNet 3D" Firmware. There are also a few things to consider when it comes to the sensors themselves. The best way to choose a capacitive sensor is to print on a glass surface, as an inductive sensor does not recognize glass. An inductive sensor, on the other hand, usually works more precisely, but mainly detects metallic objects. You should also pay attention to the voltage with which the proximity switch is operated. Most of the time, the sensors are operated with 6 to 36 volts. Individual sensors can also be operated with just 5 volts, but measurement errors are not uncommon. So that the sensor is correctly recognized by the Anet mainboard, it is advisable to put an optocoupler in between so that no residual voltage remains when switching.
Glass plate as printing surface: If the filament doesn't want to hold properly, or if you don't have to constantly change the blue tape, we recommend switching to glass as the printing surface. A suitable pane of glass (215 x 215 mm) can be cut to size at most specialist dealers. Alternatively, you can buy a borosilicate glass plate that has already been cut to size. The advantage of glass is the very good hold, that it is easy to clean and that you get a very smooth print result. If the print does not adhere directly to the glass, you can help with a little hairspray, which creates a better floor structure. If the filament does not adhere even then, it helps to cover the glass surface with a thin layer of UHU-Stic. Every filament that is difficult to adhere is guaranteed to hold!
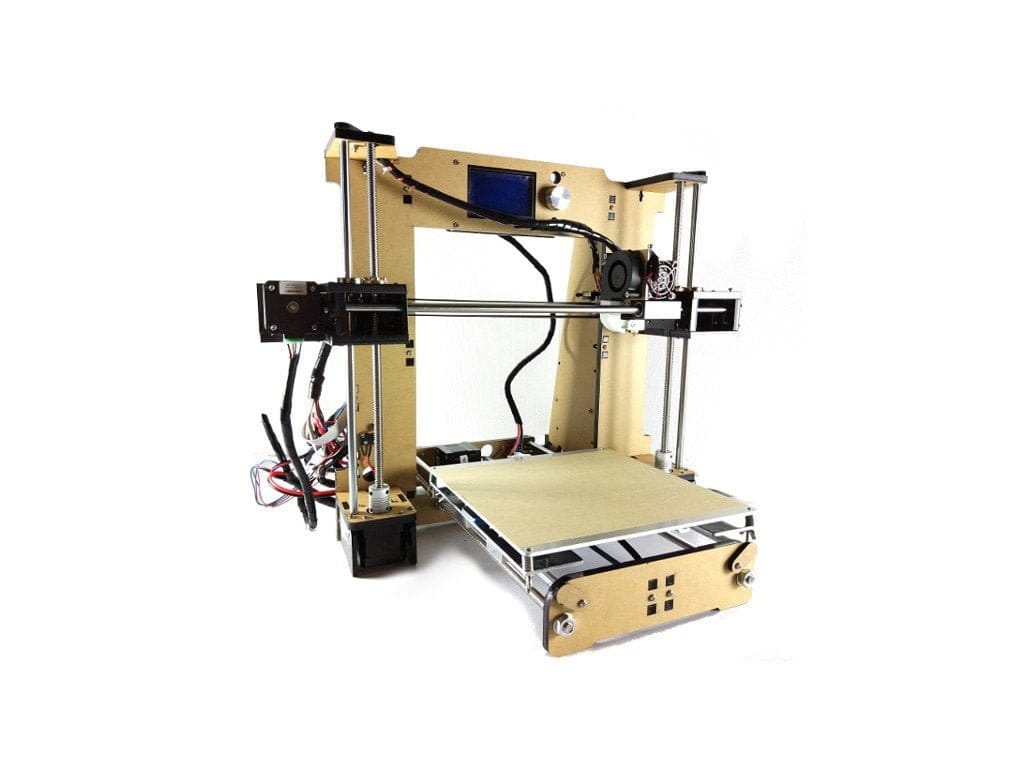
Anet A6
Good print quality
Large print area
High modification potential
Price
Quality control
Faulty building instructions
Setting down and releasing is not possible with the Anet A6. With this 3D printer, you have to lend a hand, because you only get the components that are needed to assemble a printable 3D printer. The beginner friendliness is mediocre. The construction manual is partly faulty and you should read in the topic "Anet A6" first in detail. Even after the 3D printer has finally been assembled after hours, it is still necessary to calibrate and adjust to achieve clean print results.
However, if you like to tinker and enjoy the DIY hobby, the Anet A6 is one of the cheapest ways to assemble a printable 3D printer. If you were to buy all the items separately, you would end up probably more expensive, as if you buy the same Anet A6 Print Kit. The Anet A6 and A8 printer kits are currently being produced to cover their costs. But Anet also waives the support and unfortunately also suffers the quality control. Although you can be lucky and all parts are delivered accurately, it is also possible to get a kit with eg bent shafts, faulty threads or a crooked heatbed.
In summary, however, the Anet A6 Printer Kit pays off. The modification potential is limitless and the print quality is convincing. If you want to get low-priced 3D printing, you should definitely consider the Anet A6 Printer Kit!
seb
6. April 2017 15 to: 09
In your videos you have a glass plate on the print bed. Which one is it and where do you get it? thanks
Timo admin
10. April 2017 14 to: 12
Hi, I cut the glass plate myself from a picture frame glass. Cost about 3 €. You can of course also buy cut-to-size panels, but they are a lot more expensive. You can also get a glass cutter for just a few euros.
Markus
11. April 2017 12 to: 40
Hello, have you tried SkyNet with the Anet A6? I ordered the sensor yesterday, but don't know what exactly to do with it. Can I connect it directly or do I need an optocoupler, as you write?
Timo admin
11. April 2017 13 to: 36
Hi, SkyNet I will flash the days. I had still waited because the LJC18A3-HZ / BX was sold out on Amazon with delivery from DE (but now available again!). I have the sensor here now. Which one did you order? The LJC18A3-HZ / BX NPN NO could possibly even be operated with 5V without an optocoupler. I have no idea how imprecise the measurement results are. But I'll try that out.
Peter Markwart
3. September 2017 14 to: 33
To the point! Thank you very much for this detailed Anet A6 review. I've just ordered the printer from Gearbest and I'm really excited. How long do you think the shipping will take?
Stephan K.
14. December 2017 11 to: 43
Hallo,
First of all, many thanks for the detailed test, which helped me a lot with my first steps with the Anet A6. From my experience with the printer, I'd like to post one here, maybe it will help one or the other.
Interchangeable improvements:
1. In my opinion, another holder for the heatbed should be at the top of the list. The supplied "H" is much too soft and weak. It warps itself permanently a) when it heats up and b) under the tension of the springs and screws for adjusting the bed. I have replaced the holder with this one and am very satisfied with the result: ruthex Heatbedholder - Anet A8 A6 E10. Costs around 30 euros at a large internet retailer. Not cheap, but also worthwhile because of the included plates, which can be screwed between the holder and the Y-belt attachment to improve the belt guide.
2. Replacement of the springs for the heating bed adjustment with silicone buffers. Advantage: Feathers under constant pressure wear out and become soft. The bed often has to be readjusted. Silicone improves the stability enormously. Suitable buffers are available here, for example: https://shop.bohrers.de/silikonpuffer-4stk.html
3. Silcawool insulation, double heating bed and heating bed holder. This ensures less heat loss and faster heating-up time for the heating bed. A suitable mat in the size of a heating bed is available here, for example: https://shop.bohrers.de/heizbettisolierung-silcawool-220-220-13mm-285.html
Together with 15mm silicone buffers and the new heated bed holder, it ensures great printing results for me.
4. Alternative to the borosilicate glass plate: I treated myself to the Anycubic glass plate (ANYCUBIC Ultrabase 3D). This is simply glued to the aluminum bed. In addition, it has beveled edges, through which you can get to the screws of the heating bed even when the plate is mounted.
With this glass plate you can do without any additional adhesion improvers (hairspray, UHU glue stick or similar). I print PLA at a bed temperature of 50-60 degrees. The PLA sticks firmly to the glass plate (provided everything is adjusted correctly). If the heating bed has cooled down to around 30 degrees after printing, the printed object will detach itself from the glass surface and can simply be removed. Since mine doesn't need any additional adhesion improvers, the glass plate actually always stays clean and rarely needs to be cleaned with alcohol / glass cleaner.
Printable improvements:
1. A6 Flexible Filament Guide: https://www.thingiverse.com/thing:2242903
This is actually intended to simplify the processing / insertion of flex filament, but it also makes it much easier to change filament from normal filament. The method, also described in this article, of first pushing the filament through the hot nozzle and then pulling it up out of the extruder with a jerk, ended in 7 out of 10 attempts with a blocked extruder (or throat to the nozzle). Having to dismantle the extruder every time you change the filament is annoying. With this printable extension, filament changes now work without any problems. I cut the filament over the entry into the extruder and let the extruder (of course with a hot nozzle) extrude filament until nothing comes out at the bottom (about 40-50mm). Then I insert the new filament at the top so that it is just gripped by the extruder and let it extrude again. The new filament is straightened slightly by the extruder as it is pushed down and then pushes the old filament out of the nozzle. Of course, you have to extrude until the new filament comes out at the bottom. Of course, this type of filament change costs more filament (about 5 cm from the old and a few cm from the new) than if you pull the filament upwards. It's worth it to me, though, because I don't have to constantly dismantle the extruder.
A few more comments on the article:
1. There is no Anet Board V2.0. The version number shown in the display relates to the firmware. The board is still version 1, possibly extended with a revision number. The board that I supplied with my A6 in November still had "V1.0" on the board, the one that I also ordered for test and handicraft work had "V1.5" printed on it.
2. GT2 belts and pulleys: Only installing pulleys with 20 teeth / inch does not help at all, as the belt supplied has 16 teeth / inch. You also have to change the straps. In addition, it should be URGENTLY pointed out that the settings for the steps per mm in the printer settings must be adjusted. If you continue to print with the settings for the old belts with 16 teeth, the printed parts will be too large. The settings for the X and Y axes must be changed to 80 steps / mm so that the prints fit (in terms of size) again.
3. Y-Belt Tensioner: Belt tensioners like the one linked above should not be used without a so-called "Frame Brace" such as this one: https://www.thingiverse.com/thing:1896013
Such a reinforcement ensures that the front fastening plate, on which the belt tensioner is located, does not bend in the middle (due to the pressure of the screw) and may even break if the screw is accidentally over-tightened.
Oh, and another tip from my own experience: If the printouts do not turn out as expected because individual layers are shifted again and again, check all other possible sources of error (belt tension, loose screws, shifting axes on which the print head and heating bed are running etc.) also whether the hotend wobbles. The printhead comes fully assembled with the kit, but that does not mean that it is assembled correctly. At the hotend there is a nut which is supposed to sit as a counter nut under the plate through which the hotend is led to the extruder (print head slide). My mother was right on the heating block, i.e. at the wrong end of the hotend. As a result, when the print head moved quickly, it wobbled back and forth like a lamb's tail, which ultimately led to the shifting of individual layers during printing. After I properly tightened the nut under the printing carriage, the printer now prints really well.
Timo admin
14. December 2017 12 to: 10
Hi Stephan, thank you very much for the very detailed article and the useful tips. I added the steps for pulley and timing belt change above. In winter I will certainly have more time for the A6 again. Then the article will be completely revised :).
Thomas H.
6. February 2018 10 to: 41
Hallo,
I am currently building my Anet A6 and would install the improvements you mentioned right from the start.
Did you just swap the shafts of the X-axis for the precision shafts made of aluminum or also those of the other axes?
Thank you and best regards
Oswald Brotschinsky
6. April 2018 17 to: 36
Thanks, that was extremely helpful.
Kek44
28. May 2018 06 to: 47
Hallo,
I have the problem that the bracket for the X-axis goes into the ceiling at the top, i.e. into the screws at the top or, if you remove them, into the acrylic.
So I don't get to 240mm at all (250 is not even in the firmware, verifiable in the manual position adjustment mode)
Is there a solution for this?
In addition, it is never 500g. Maybe 50?
How did you lay the cables from the extruder to the mainboard? For me, they get stuck between the left rods and the extruder